Published on June 25, 2021
Hatchery hygiene, part 1 Prevention
The basis for running a successful hatchery lies in having a healthy breeding flock, a clean hatchery with clear processes and dedicated people taking good care for the birds their health and welfare and following the processes to safeguard optimal quality during all processes, from breeder flock management, to hatching egg collection and storage and incubation and chick handling. Any deviation during the process can result in poorer bottom line results. In this paper we provide practical know-how to improve hatchery hygiene as this is such an important process that contributes to the success of the hatchery.
Poor hatchery hygiene may result in reduced hatchability and chick quality and consequently considerable economic losses. Additionally, hatchery hygiene plays an essential role in the efficiency and safety of the poultry production chain. Without proper control, pathogens will multiply and spread within the hatchery, potentially putting many if not all customers at risk, especially where contamination presents a health hazard for the consumer by food-borne infections, such as Salmonella and Campylobacter. More common bacteria, like E. coli spp. can cause increased seven-day mortality, with suboptimal production and the need for the increased use of antibiotics. Ultimately, the hatchery’s reputation may be jeopardized - and restoring the customer’s confidence is much harder than maintaining it. It is therefore key to prevent the spread of pathogens inside the hatchery at all times. The hatchery should have a hygiene program designed to minimize the level of micro-organisms in the hatchery.
Optimized hygiene in the hatchery is dependent on three key areas:
- preventing pathogens from entering the hatchery, i.e. maintaining biosecurity
- avoiding cross-contamination or the transfer of pathogens within the hatchery, and
- inhibiting further pathogenic development in the hatchery i.e. cleaning and disinfection
The prevention of pathogens entering the hatchery
Good hatchery hygiene begins with preventing the introduction of pathogens into the hatchery. Pathogens can be carried into the hatchery by various vectors. We will describe the main vectors and provide recommendations on how to prevent the introduction of pathogens through these vectors.
Hatching eggs including transport equipment: this is one of the most obvious vectors for the introduction of pathogens are the hatching eggs and egg trays. Floor eggs and dirty eggs should not be considered as hatching eggs and therefore should stay out of the hatchery, particularly because they are potential exploders. It is important that hatching eggs are well supported during transport to avoid hairline cracks, which provide unchecked entry points for bacteria and fungi to get inside the egg. Once the shell - a critical defense mechanism - is breached, the result is not only loss, but also a serious breach in hatchery biosecurity. Purpose designed setter trays for on-farm traying are a perfect alternative to the single use of pulp trays. In any case, only new pulp trays should be used – and setter trays and farm trolleys should be cleaned and disinfected between each use. Vertical transmission, from breeder hen to day-old-chick by egg yolk contamination, of specific pathogens like Salmonella enteritidis and Mycoplasma gallisepticum can only be prevented by strict monitoring of the breeder flock.
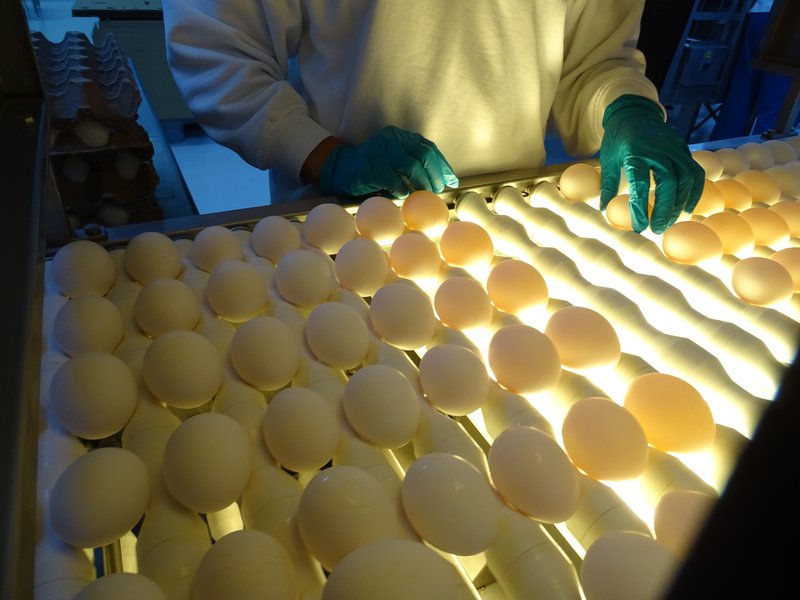
Careful checking of the hatching egg quality for hairline cracks and dirt prior to setting the eggs is strongly recommended
Hatchery staff and visitors: to avoid people acting as vectors and bringing pathogens into the hatchery, a well-designed entrance facility is essential. The following facilities are highly recommended to have in place:
- a wardrobe for clothing and shoes worn outside the hatchery
- a clean shower (soap, hot and cold-water tap)
- a clear separation between the “clean” and the “dirty” area
- a wardrobe with clean, disinfected clothing and footwear to be worn inside the hatchery
Any area accessed prior to the changing rooms and showers in a hatchery should be regarded as a ‘dirty area’, with the ‘clean area’ of the hatchery incorporating the setter room, candling and transfer room, hatcher rooms and chick handling and dispatch rooms at minimum.
Technical areas should be located at the outside of the building, so that engineers have no cause to enter the clean area. Similarly, offices for administrative personnel and canteens for truck drivers should be clearly and effectively separated from the clean areas. Only necessary visitors should be allowed into the hatchery. Visitors should sign in their name + date of last contact with live poultry (use a visitor registration form) and let them follow the same hygiene instructions applying to hatchery personnel.
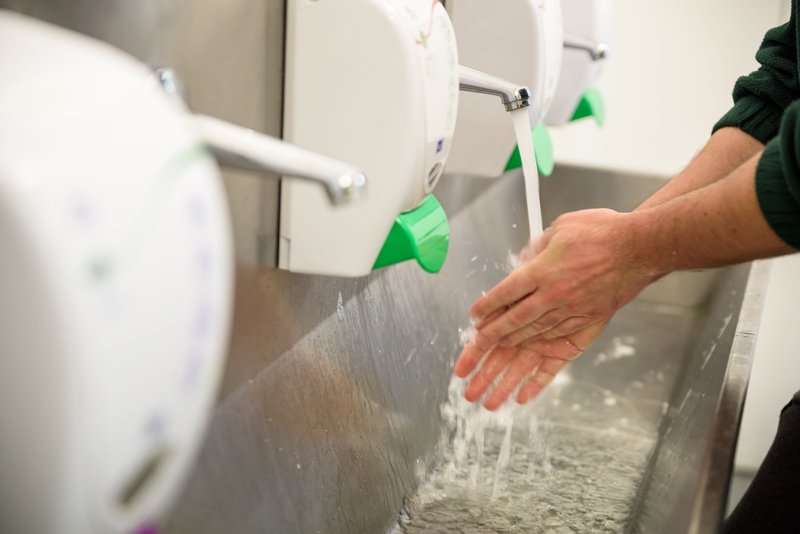
Washing hands, one of the cheapest and most effective practices to remove pathogens
Air: the hatchery design is key in hatchery hygiene; proper prevention begins when designing a new hatchery project. The location should be carefully chosen, taking the position of nearby poultry farms and public roads in relation to prevailing wind direction into consideration. Air filters in the air handling unit(s) minimize the introduction of pathogens (they are often attached to dust particles), into the hatchery. If you want to achieve a higher level of protection it is advised to install biofilters.
Rodents: Strict rodent control, based on continuous prevention and monitoring, is essential to keep them out of the hatchery. Prevention starts with keeping everything (including the surroundings) neat and tidy, avoiding the attraction of rodents with food such as hatchery waste. Monitoring should be based on observing the signs of rodent presence – like footprints and droppings. Outsourcing of rodent control could be considered.
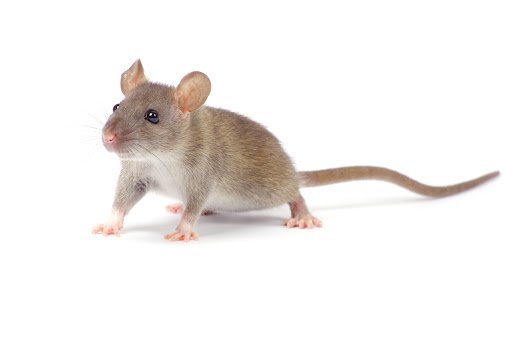
Monitoring should not only be based on observing of the rodents, but also on their signs – like footprints and droppings.
Other vectors Pathogens could enter the hatchery in or on other vectors, such as water, wild birds, beetles, cats and dogs, contaminated paper chick boxes (e.g. Aspergillus) or dirty chick boxes after a previous chick delivery. One should be alert for each of these vectors and take adequate action if required.
The prevention of cross contamination
For good hatchery hygiene, it is vital to prevent contamination spreading from one room to another inside the hatchery. To prevent cross-contamination, it is important to clearly distinguish between different hygienic zones inside the hatchery:
- hatching egg arrival area
- setter room
- candling/transfer room
- hatcher room
- chick handling and dispatch room
The processes in the hatchery should be carried out according to a one-way traffic system in line with the egg flow through the hatchery: clean should never meet dirty. Some examples, the hatchery manager who first looks in the chick handling room and moves from there straight, without changing clothes and showering to the setter room acts as a vector for micro-organisms. Or eggs being transferred to the hatcher do not cross the path of chicks just being pulled out of hatchers, and hatcher baskets, after being washed and disinfected, do not pass through the chick room, or any area where processing takes place, on their way to the transfer room. A well-designed hatchery and different colored hatchery clothing and shoes, as well as tools such as floor scrubbers, greatly help to enforce hygiene responsible behavior.
Chick fluff (down) is another potential contaminant - and easily becomes airborne. Its movement must therefore be controlled to prevent cross-contamination. Keep doors closed to prevent cross-contamination between hatchers and the different rooms. The setter room should be maintained as the cleanest room in the hatchery and has therefore the highest pressure. The accumulation of chick fluff in air ducts is to be avoided because this can create ideal breeding grounds for molds like Aspergillus. Air leaving the hatcher, and preferably also the setter, should be brought directly into exhaust plenums which can be easily cleaned and disinfected.
Exploders, often caused by Pseudomonas spp., are an important source of cross-contamination between batches within the same setter. To reduce this risk, batches with an increased incidence of exploders should be transferred to the hatcher last. Potential exploders are often recognized by a foamy substance oozing from the pores in the shell; carefully try to dispose them prior to transfer.
Strictly applying the “One batch per hatcher” rule, enabled by limiting the capacity of the hatchers, greatly prevents the risk of cross contamination, for example from older to younger batches. In a well-designed hatchery the number of hatchers per hatcher room is based on the daily production of chicks. This avoids recontamination after cleaning and disinfection, and thus minimizes the risk of contaminating the next day’s hatch.
To conclude
Hatchery hygiene is essential when the goal is to optimize chick quality. A well-functioning hatchery hygiene program helps to prevent economic losses and contributes to the safety of the entire poultry production chain. Do not see it as a cost but as an investment, a proper functioning hatchery hygiene program pays itself back immediately. The goal of your hatchery hygiene program should be on the prevention of pathogens from entering and the inhibition of pathogen development to optimize the hygienic status of your hatchery. Frequent monitoring of the different hygiene processes is essential and do take corrective action to achieve the required improvement. Better chick quality tomorrow starts with a cleaner hatchery today!
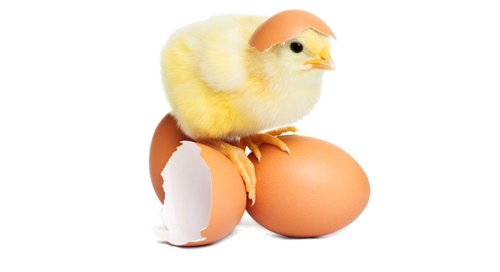
Chick quality starts with good hatchery hygiene!